Table of Contents
1. Introduction
2. The Baltimore bridge collapse: a wake-up call
3. Understanding supply chain resilience
4. Industries hit hard by the Baltimore port closure
5. Building a resilient supply chain: best practices
6. Conclusion
Introduction
The collapse of the Francis Scott Key Bridge in Baltimore sent shockwaves through the business community, exposing the fragility of our supply chains in the face of unexpected disruptions. As a business professional or online retailer, you understand the critical importance of maintaining a steady flow of goods to meet customer demands and keep your operations running smoothly. The Baltimore incident serves as a stark reminder that building supply chain resilience is not just a buzzword, but a strategic necessity in today’s unpredictable landscape. In this article, we’ll explore the concept of supply chain resilience, examine the industries most affected by the Baltimore port closure, and share best practices for fortifying your own supply chain against future disruptions.
The Baltimore bridge collapse: a wake-up call
The Francis Scott Key Bridge in Baltimore, a vital link for commuters, tourists, and businesses, collapsed after being struck by a vessel, resulting in a tragic loss of life and widespread disruption. The incident immediately impacted traffic and transportation in the region, forcing individuals and freight carriers to seek alternative routes. Moreover, the bridge carried critical utility lines, including water, gas, and fiber optic cables, which were severely damaged or severed, compounding the challenges faced by local residents and businesses.
The collapse also dealt a significant blow to the Port of Baltimore, one of the busiest and most important ports on the East Coast. Handling approximately 11 million tons of cargo annually, including automobiles, containers, coal, and agricultural products, the port relies heavily on the bridge to connect its rail network and interstate highway system. The port’s closure, while temporary, had far-reaching economic and environmental consequences, as well as implications for national security and defense.
Although neighboring ports, such as Norfolk, Virginia, and New York City, were able to absorb the additional traffic without major complications or delays, the Baltimore bridge collapse served as a wake-up call for businesses across the nation. It underscored the vulnerability of our aging infrastructure and the paramount importance of building supply chain resilience in the face of unforeseen disruptions.
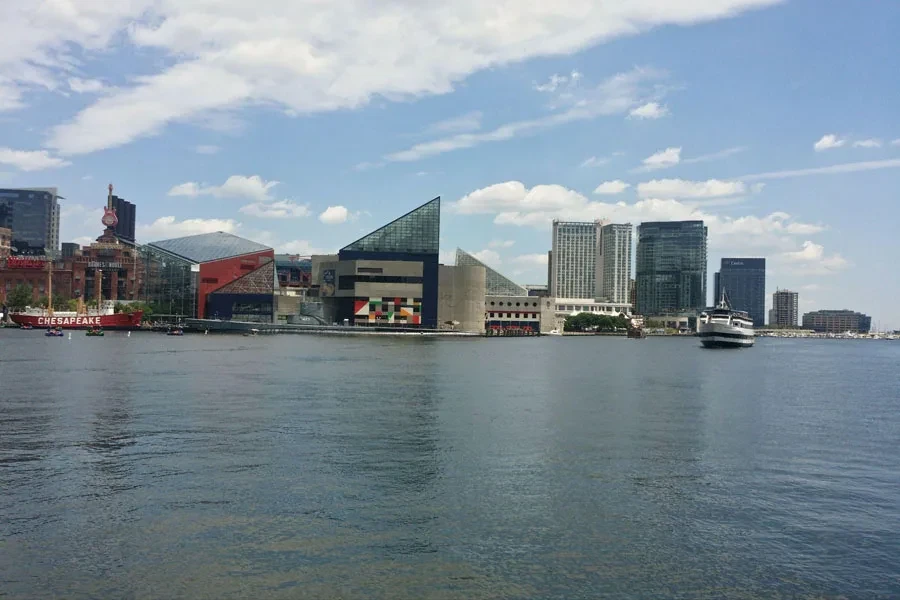
Understanding supply chain resilience
Supply chain resilience is a multi-faceted concept that encompasses a supply chain’s ability to withstand, adapt to, and recover from disruptions. Christopher and Peck, in their 2004 work “Building the Resilient Supply Chain,” propose four key dimensions of resilience: robustness, agility, redundancy, and flexibility.
Robustness refers to a supply chain’s ability to maintain normal operations in the face of disruptions. This is achieved through strong, reliable infrastructure, equipment, technology, and human resources capable of withstanding shocks and stresses. Agility, on the other hand, is the supply chain’s capacity to respond swiftly and effectively to disruptions, restoring functionality and performance. Agile supply chains leverage real-time data, advanced analytics, and cross-functional teams to identify and resolve issues promptly.
Redundancy involves maintaining extra or alternative resources and options to mitigate the impact of disruptions. This may include safety stocks, contingency contracts, multiple sourcing, and diversified networks, ensuring the continuous availability of goods and materials. Lastly, flexibility refers to a supply chain’s ability to adjust its structure, processes, or products in response to disruptions, adapting to changing customer needs, market conditions, or environmental factors.
To build true resilience, businesses must strive for a balanced, integrated approach that incorporates all four dimensions. By proactively anticipating potential disruptions and continuously learning from past experiences, companies can develop a supply chain that not only survives but thrives in the face of adversity.
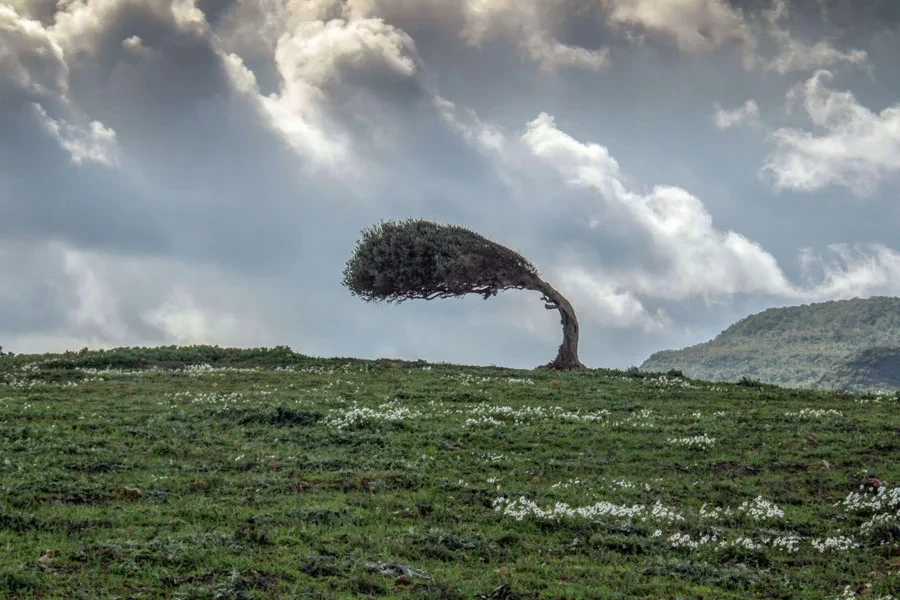
Industries hit hard by the Baltimore port closure
The Port of Baltimore’s closure following the bridge collapse had a profound impact on several industries that rely heavily on the port for importing and exporting goods. The automotive industry, which uses the port to handle approximately 800,000 vehicles per year, experienced significant disruptions in the flow of vehicles and parts. This affected the operations and sales of automakers, dealers, and suppliers, creating congestion and delays at other ports and transportation modes.
The container industry also felt the effects of the closure, as the Port of Baltimore is the ninth-largest container port in the country, handling around 600,000 containers annually. The disruption impacted trade lanes and port operations, affecting the livelihoods of shippers, carriers, and terminal operators.
As the largest coal port in the United States, handling about 20 million tons of coal per year, the Port of Baltimore’s closure dealt a blow to the coal industry. The outbound flow of coal and related products, such as coke, iron ore, and steel, was disrupted, impacting the operations and profits of coal producers, exporters, and traders.
The farm industry, which relies on the port to export approximately 10 million tons of agricultural products like soybeans, corn, wheat, and poultry each year, also suffered from the port’s closure. The disruption affected farmers, exporters, and processors, as well as the flow of related inputs such as fertilizers, pesticides, and seeds.
The ripple effects of the port closure extended beyond the local and regional levels, affecting national and global supply chains. The incident exposed the vulnerabilities and interdependencies of these supply chains, underscoring the need for resilience and collaboration among stakeholders.
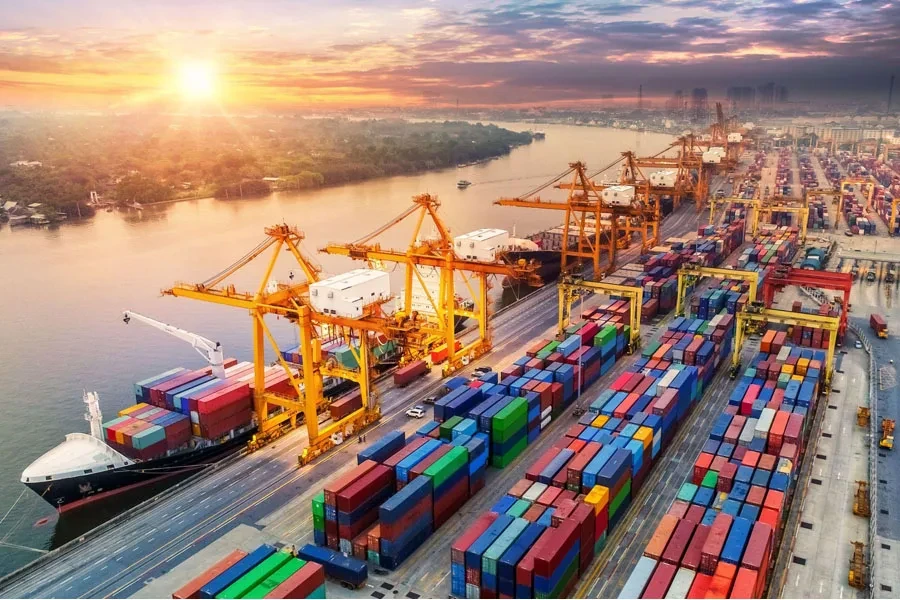
Building a resilient supply chain: best practices
The Francis Scott Key Bridge collapse and the subsequent Baltimore port closure serve as poignant examples of the myriad disruptions that can befall supply chains in an increasingly complex and uncertain business landscape. While these disruptions pose significant challenges and risks, they also present opportunities for growth and innovation. To cultivate supply chain resilience and navigate future disruptions effectively, businesses should consider implementing the following best practices:
1. Assess and monitor risks and vulnerabilities: Utilize tools such as risk matrices, scenario analyses, and stress testing to identify potential disruptions’ sources, types, probabilities, impacts, and consequences. This proactive approach enables businesses to develop targeted strategies for mitigating risks and minimizing the impact of disruptions.
2. Develop and implement contingency plans: Create comprehensive business continuity plans, establish crisis management teams, and define emergency response protocols. Clearly delineate the roles, responsibilities, and actions of supply chain stakeholders, and ensure that the necessary resources, processes, and systems are in place to effectively cope with disruptions.
3. Invest in resilience-building capabilities: Allocate resources towards developing the infrastructure, technology, human capital, and relationships that enhance the supply chain’s robustness, agility, redundancy, and flexibility. By strengthening these key areas, businesses can improve their ability to resist, respond, recover, and adapt to disruptions.
4. Learn and improve from experience: Conduct thorough post-mortem analyses following disruptions to identify lessons learned and best practices. Evaluate the effectiveness and efficiency of the supply chain’s response and recovery efforts, and pinpoint opportunities for continuous improvement and innovation.
5. Foster collaboration and communication: Prioritize information sharing, joint planning, and coordination with supply chain partners and stakeholders. Build trust, transparency, and alignment among supply chain actors to ensure a shared understanding of the interdependencies and impacts of supply chain disruptions, enabling a more cohesive and effective response.
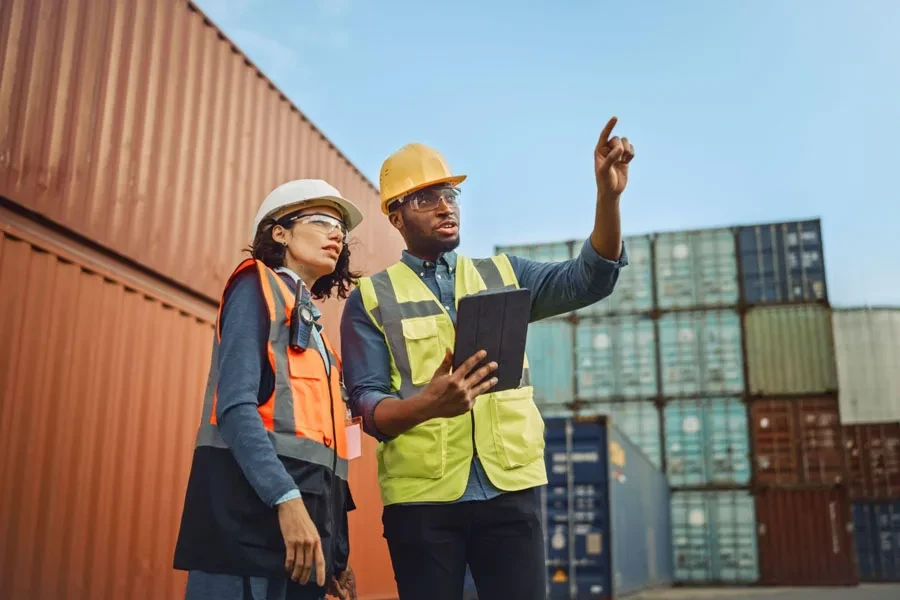
Conclusion
By embracing these best practices, businesses can cultivate supply chain resilience and position themselves to not merely survive but thrive amidst the uncertainties of an ever-changing world. In an era where disruptions are increasingly common, supply chain resilience has emerged as a strategic imperative – a vital competitive advantage that enables businesses to adapt, innovate, and succeed in the face of adversity. The Baltimore bridge collapse stands as a powerful reminder of the importance of proactive risk management and the cultivation of a resilient supply chain. By heeding the lessons of this incident and investing in the development of robust, agile, and adaptable supply networks, businesses can chart a course towards a more secure and prosperous future.
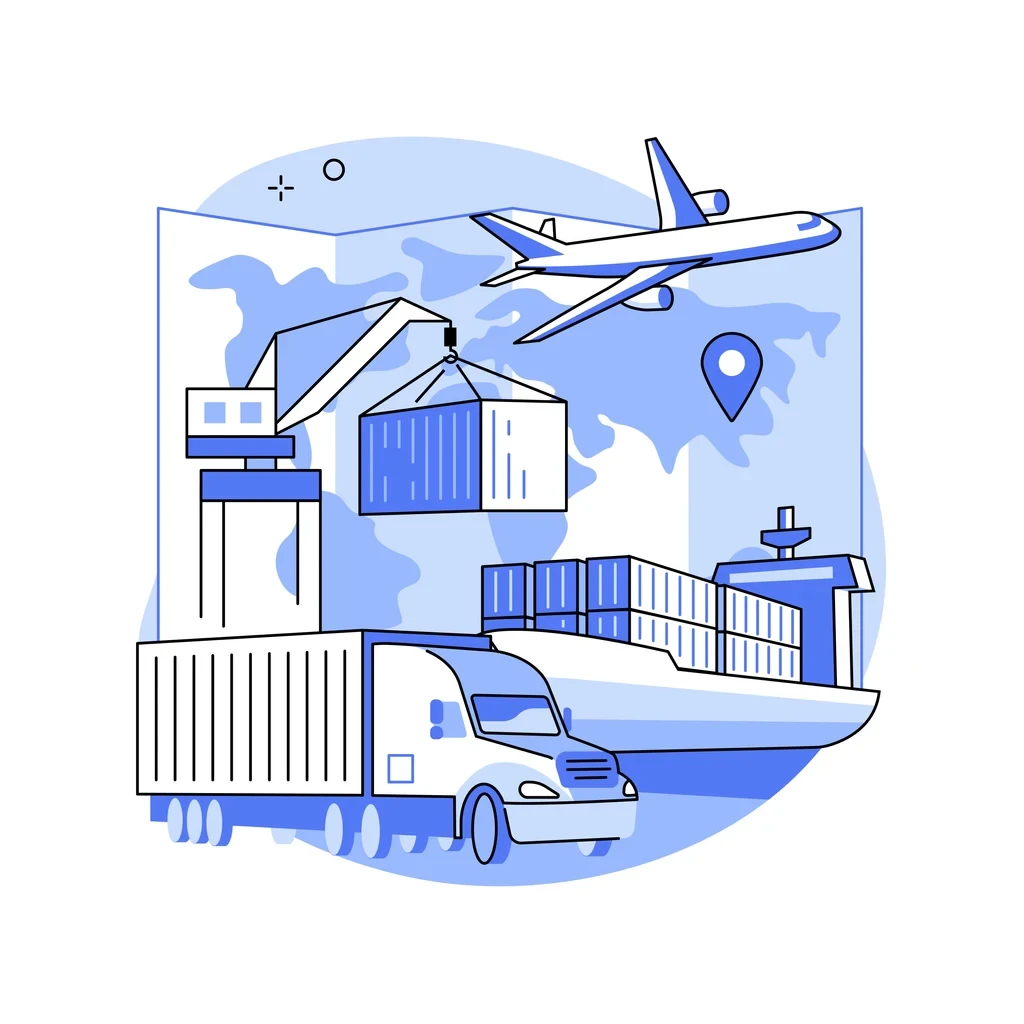
Looking for a logistics solution with competitive pricing, full visibility, and readily accessible customer support? Check out the Alibaba.com Logistics Marketplace today.